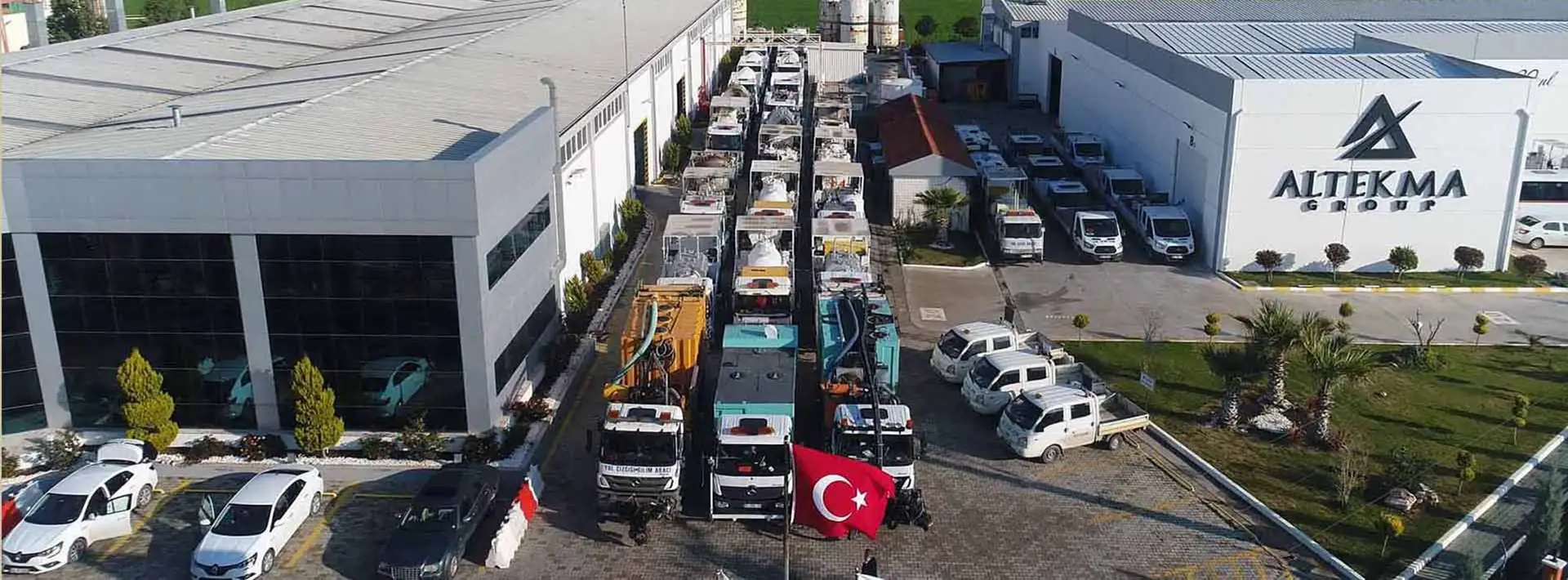
WHAT ARE THE SURFACE PREPARATION STANDARDS IN TURKEY AND THE WORLD?
WHAT ARE THE SURFACE PREPARATION STANDARDS IN TURKEY AND THE WORLD?
WHAT ARE THE SURFACE PREPARATION STANDARDS IN TURKEY AND THE WORLD?
The shot blasting process is graded according to the extent to which unwanted formations are cleaned on the surface of the steel and the extent to which the surface is abraded. There are some standard grades in the world on this subject. In Turkey, the Swedish standard "Swedish Standards For Ground Vibrations And Airblast" SA 1, SA 2, SA 2.5 and SA 3 grades are used. These ratings have been adopted by TSE as TS EN ISO 8501-1.
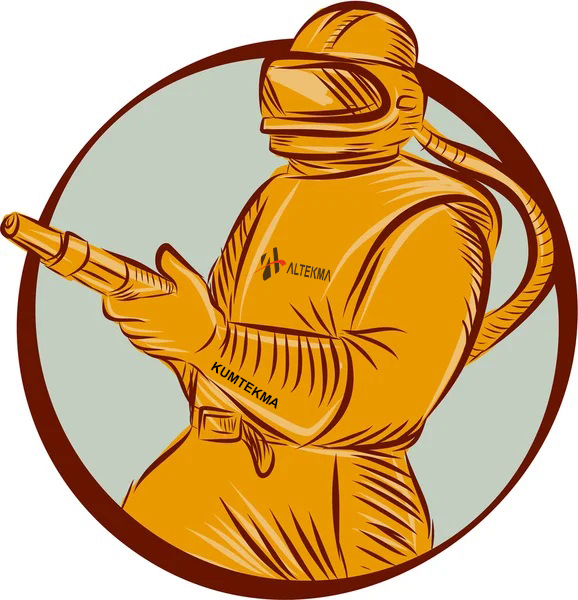
Surface preparation standards exist to minimize costs and maximize coating life. White Metal is expensive to obtain, especially in maintenance work, and is typically reserved for critical applications where the cost of failure is catastrophic. Surface preparation can be 40% of the cost of a repainting project. It is commercially suitable for non-corrosive environments and service environments. Brushing, if it can get away with it, saves money in the short term.
NACE International has recently published five new wet abrasive blasting standards. The joint NACE/SSPC: 'Society for Protective Coatings' standards defined the processes for preparing a carbon steel surface to a specific degree of surface cleanliness using wet abrasive blast cleaning. Each standard represents one of five levels of cleanliness, including white metal, near-white metal, commercial, industrial and brushing.
WHITE METAL BLASTING
Shot Blast Cleaning for Clean Steel (SP 5 / NACE #1 / SA 3)
White Metal is the highest grade of abrasive blast cleaning. No darkening, streaks or stains are allowed. When viewed without magnification, the surface must be free of visible oil, grease, dust, dirt, mill scale, rust, coating, oxides, corrosion products and other foreign matt
White metal is specified for cases where the catastrophic effects of coating deterioration may be a justification for extra cost, i.e. steels and nuclear reactors, turbines, chemical tank linings, submarines, etc. operating in high temperature, high pressure and corrosive environments.
Loosely adhered material: 0% Tightly adhered material: 0% Stains, streaks, darkness: 0%
NEAR WHITE SANDBLASTING
Very thorough Shot Blast Cleaning (SP 10 / NACE #2 / SA 2.5)
Near White Shot Blast Cleaning specifies that darkness, marks and stains should be limited to 5% of the surface area. Near White is determined when the advantage of blasting for White Metal does not justify the added expense.
Near White is typically specified for high performance coatings on steel exposed to severe environmental conditions such as chemical spills and fumes, high humidity and proximity to salt water. Often specified for oil rigs, shipyards and other marine environments.
Loosely adherent material: 0% Tightly adherent material: 0% Stains, marks, darkening: Sa 2 ½ 15
COMMERCIAL SANDBLASTING
Comprehensive Blast Cleaning (SP 6 / NACE #3 / SA 2)
Commercial Blast Cleaning determines that all tightly adhering substances must be removed. Stains, streaks and darkness may remain on up to 33% of the surface.
Commercial is determined when a high but not perfect degree of cleanliness is achieved. Widely used for repainting products in service in non-corrosive environments and atmospheres such as tanks and bridges.
Loosely adhering material: 0% Tightly adhering material: 0% Stains, streaks, darkness: 33
INDUSTRIAL SANDBLASTING
(SP 14 / NACE #8)
Industrial Blast Cleaning specifies that 90% of the tightly adhering material must be removed. 100% of the surface will have rust, mill scale and darkening, streaks and stains from old coatings.
Industrial is defined for conditions where the existing coating is thin, well adhered and compatible with the new coating. It is the latest abrasive blasting standard and is not widely specified. ISO does not have a corresponding specification.
Loosely adhered material: 0% Tightly adhered material: 10% Stains, streaks, darkness: 100%
BRUSHING
Light Blast Cleaning (SP 7 / NACE #4 / SA 1)
Brushing is designated to remove loose rust, mill scale and coatings and to evenly and uniformly roughen a surface in preparation for a new coating. Tightly adhering materials are allowed to remain.
Brushing is recommended for non-corrosive service environments where the expected coating life is short, such as ship hull anti-decay paint, or in temperate atmospheres and rural locations, such as the exterior of a tank.
Loosely adhering material: 0% Tightly adhering material: 100% Stains, streaks, darkness: 100%
The shot blasting process is graded according to the extent to which unwanted formations are cleaned on the surface of the steel and the extent to which the surface is abraded. There are some standard grades in the world on this subject. In Turkey, the Swedish standard "Swedish Standards For Ground Vibrations And Airblast" SA 1, SA 2, SA 2.5 and SA 3 grades are used. These ratings have been adopted by TSE as TS EN ISO 8501-1.
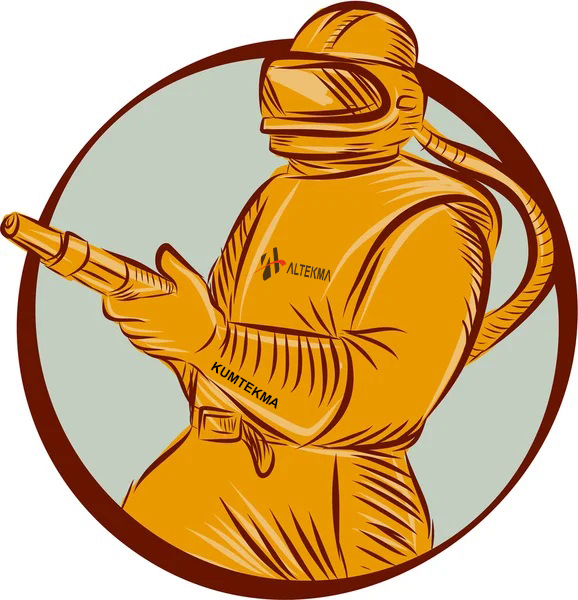
Surface preparation standards exist to minimize costs and maximize coating life. White Metal is expensive to obtain, especially in maintenance work, and is typically reserved for critical applications where the cost of failure is catastrophic. Surface preparation can be 40% of the cost of a repainting project. It is commercially suitable for non-corrosive environments and service environments. Brushing, if it can get away with it, saves money in the short term.
NACE International has recently published five new wet abrasive blasting standards. The joint NACE/SSPC: 'Society for Protective Coatings' standards defined the processes for preparing a carbon steel surface to a specific degree of surface cleanliness using wet abrasive blast cleaning. Each standard represents one of five levels of cleanliness, including white metal, near-white metal, commercial, industrial and brushing.
WHITE METAL BLASTING
Shot Blast Cleaning for Clean Steel (SP 5 / NACE #1 / SA 3)
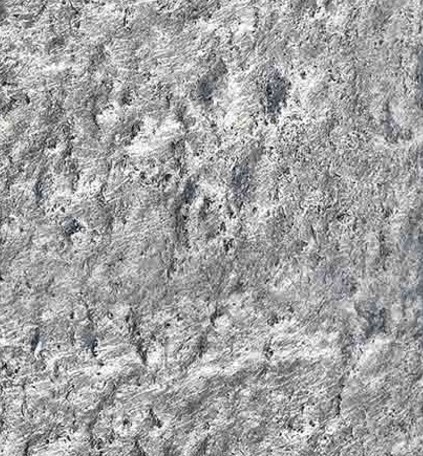
White metal is specified for cases where the catastrophic effects of coating deterioration may be a justification for extra cost, i.e. steels and nuclear reactors, turbines, chemical tank linings, submarines, etc. operating in high temperature, high pressure and corrosive environments.
Loosely adhered material: 0% Tightly adhered material: 0% Stains, streaks, darkness: 0%
NEAR WHITE SANDBLASTING
Very thorough Shot Blast Cleaning (SP 10 / NACE #2 / SA 2.5)
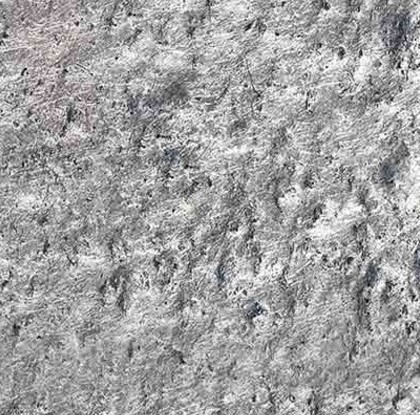
Near White is typically specified for high performance coatings on steel exposed to severe environmental conditions such as chemical spills and fumes, high humidity and proximity to salt water. Often specified for oil rigs, shipyards and other marine environments.
Loosely adherent material: 0% Tightly adherent material: 0% Stains, marks, darkening: Sa 2 ½ 15
COMMERCIAL SANDBLASTING
Comprehensive Blast Cleaning (SP 6 / NACE #3 / SA 2)
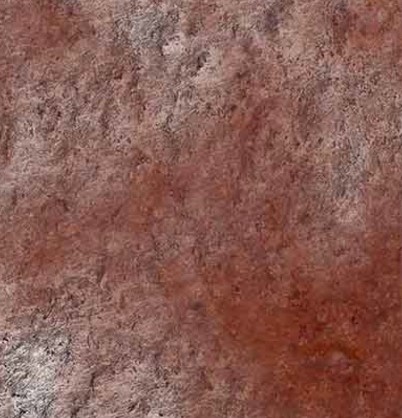
Commercial is determined when a high but not perfect degree of cleanliness is achieved. Widely used for repainting products in service in non-corrosive environments and atmospheres such as tanks and bridges.
Loosely adhering material: 0% Tightly adhering material: 0% Stains, streaks, darkness: 33
INDUSTRIAL SANDBLASTING
(SP 14 / NACE #8)
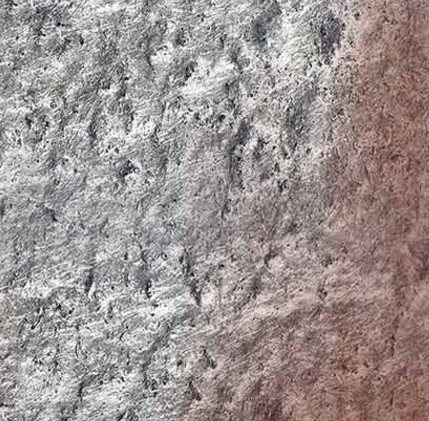
Industrial is defined for conditions where the existing coating is thin, well adhered and compatible with the new coating. It is the latest abrasive blasting standard and is not widely specified. ISO does not have a corresponding specification.
Loosely adhered material: 0% Tightly adhered material: 10% Stains, streaks, darkness: 100%
BRUSHING
Light Blast Cleaning (SP 7 / NACE #4 / SA 1)
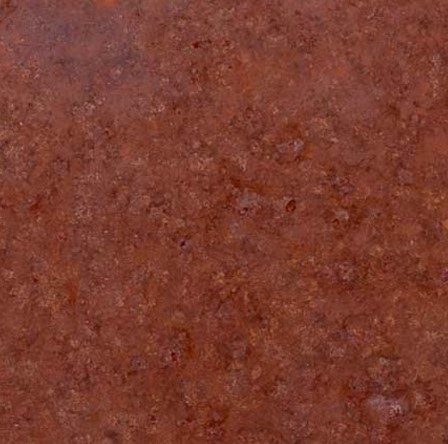
Brushing is recommended for non-corrosive service environments where the expected coating life is short, such as ship hull anti-decay paint, or in temperate atmospheres and rural locations, such as the exterior of a tank.
Loosely adhering material: 0% Tightly adhering material: 100% Stains, streaks, darkness: 100%